top of page
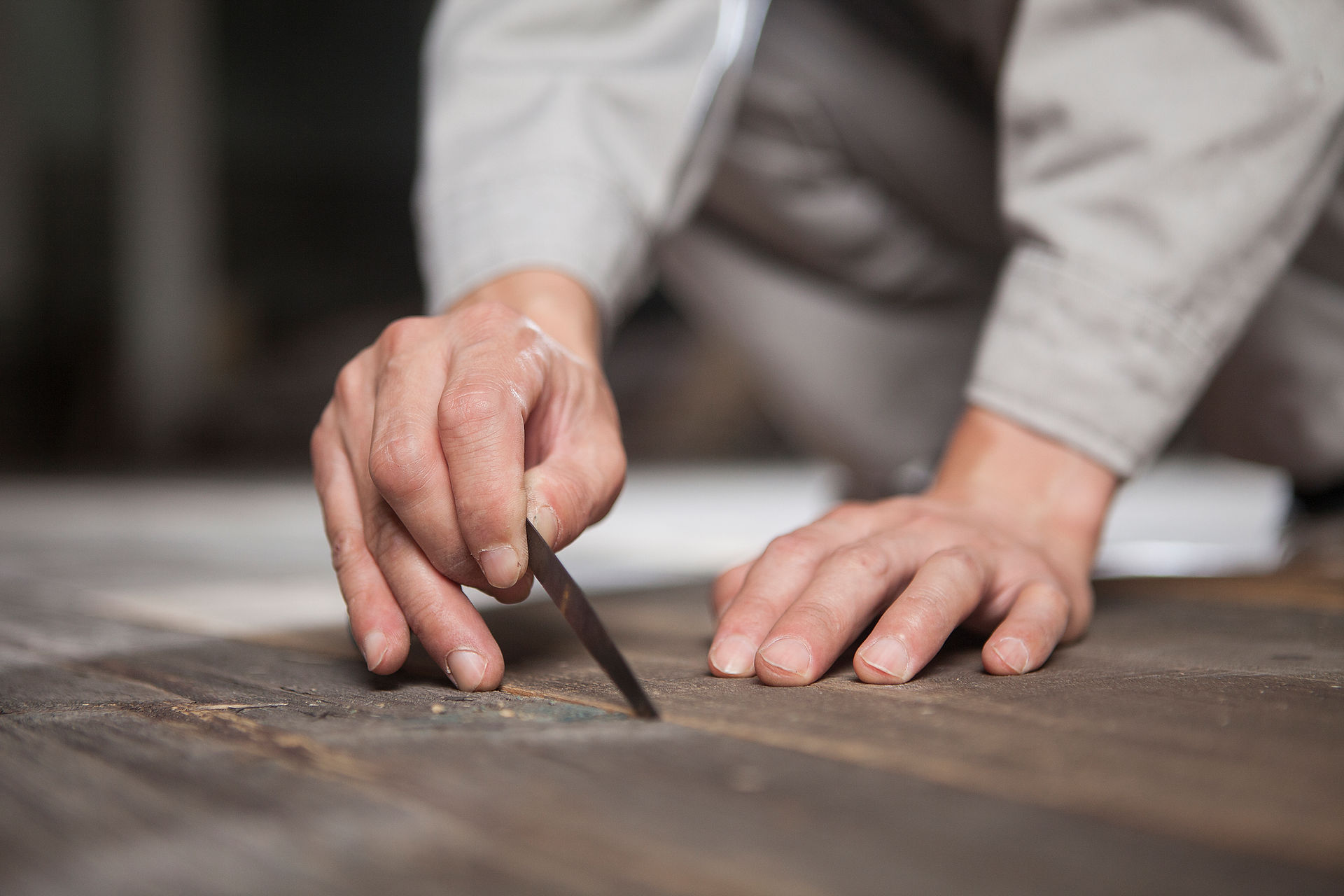
Bucket Saw Project: Designing an attachment to turn a jigsaw into a scroll saw
This was a part of Design Studio IV(Integrated Design) and the goal of the Bucket Saw Project was to design an attachment to turn Milwaukee 6268-21 Orbital Jig Saw and a 5-gallon plastic bucket into an affordable, transportable, and useful scroll saw.
​
Skills Learned:
-
Injection Molding Design Requirements
-
SolidWorks drafting for injection molding
-
Axiomatic Design Evaluation
-
Lifestyle Board Creation
-
Working with real companies


Details:
​
Aesthetic of Target Community
The target audience of our bucket saw is anybody who does extensive work around the house. This bucket saw is mainly designed to be used in a garage at home or maybe even outdoors if it’s nice outside. It is a very low budget addition so it can be afforded by almost any social status. Since it takes some effort and time to construct the bucket saw, it is recommended for people who cut wood frequently and not somebody who would use it rarely. In addition, the bucket saw is not designed to make precise cut. It is designed for quick and proficient cut. Therefore, it is suited for entry-level DIY projects that does not require heavy-duty machineries.
​
Major Objective of the Project
The Bucket Saw project allowed us to go through the design process with injection molding of plastic in mind. Therefore we spent significant amount of time considering the DFM of our design. Along side this, we utilized a method called Axiomatic Design to evaluate the level of our design by comparing the functional requirements and the corresponding design parameters.

Our Solution:
​
Our solution was to design a circular work table with inch apart ribs for structural support, DFM for injection molding, and visual cutting guide. With the use of transparent plastic, we were able to make structural design into a design feature.
​
The jig saw is secured into place with four screws directly into the work table with existing threads on the jig saw. The work table and the bucket is connected and secured by two-piece locking system (ring and a clip) that is similar to commercial storage unit.
​
We were able to estimate the cost of each unit by working with an injection mold maker called Protolabs. Our unit cost for injection molded parts alone was $33.27.
​
Based on our math models, we identified few problems for future improvements. However, due to limited time of the project (2 weeks), we were not able to make these changes to our final design at the moment.
​
See Engineering Details page below to read detailed description of each stage and design descriptions
Engineering Detail
bottom of page